PCB Prototype
Rely on MOKO to Get Quick-Turn, Reliable, and Professional PCB Prototype Services
Why Choose Us?
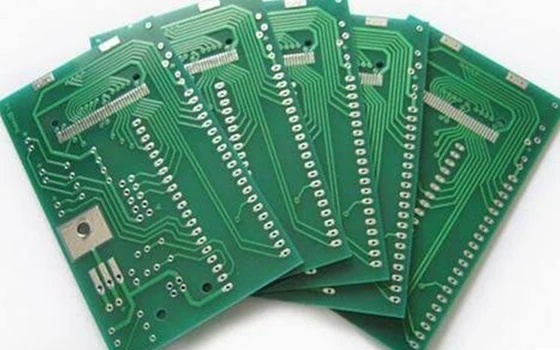
Various PCB Prototypes Available
A variety of PCB prototypes can be manufactured based on your requirements, whether single or double-sided PCB, blind or buried via boards, boards made with different materials or rigid-flex PCB and rigid PCB, MOKO Technology has got you covered.
Quick Turnaround
MOKO provides quick-turn PCB prototypes service, our factory is equipped with 5 STM lines and 3 DIP production lines, therefore, we have flexible productivity to handle prototypes of different complexity, for common PCBs, we can deliver prototypes within 24 hours.
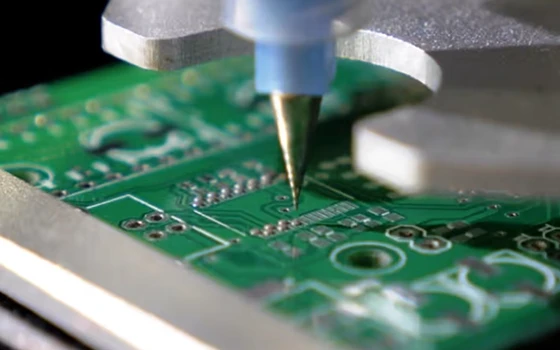
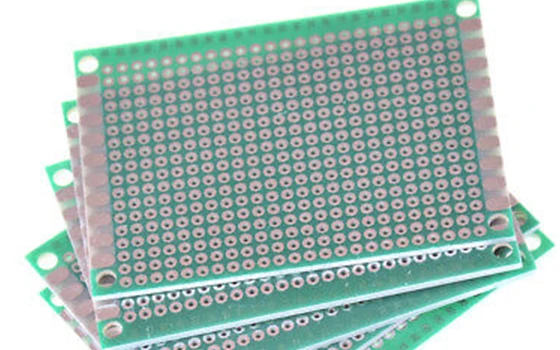
Quality Control
We have a set of strict quality control system to ensure that every process will be carried out in accordance with IPC standards. We provide our customers with prototypes that exactly meet customer needs and meet the highest quality standards.
Benefits of PCB Prototype
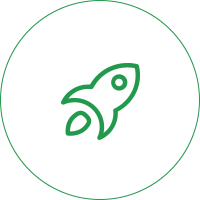
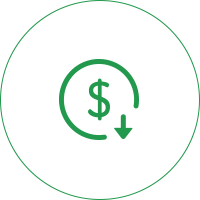
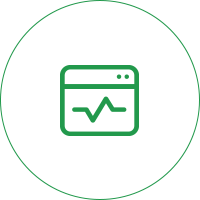
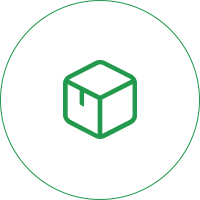
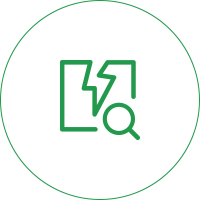
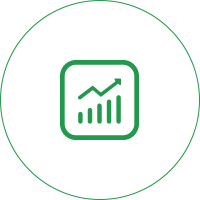
Our Capabilities
- Quality Grade:
- Board Thickness Tolerance:
- Board Side:
- Min. Drilled Hole Size:
- Min. Line Spacing:
- Hole Tolerance:
- Standard IPC 2
- ±0.1mm - ±10%
- Min 6*6mm | Max 500*500mm
- 0.25mm
- 0.075mm (3mil)
- PTH: ±0.075, NTPH: ±0.05
- Available Layers:
- Board Thickness:
- Board Size Tolerance:
- Min. Line Width:
- Surface/Hole Plating Thickness:
- Solder Mask Color:
- 1~40 layers
- 0.2mm~7mm
- ±0.1mm - ±0.3mm
- 0.075mm (3mil)
- 20μm - 30μm
- Green/Black/White/ Red/Blue/Yellow
- Material:
- Surface Treatment:
- FR-1, FR-2, FR-4, FR4 Halogen Free, CEM-1, CEM-3, Hight TG, Aluminum
- Immersion gold Immersion, HALS/HALS lead free, Chemical tin, Chemical Gold
PCB Prototype Cases
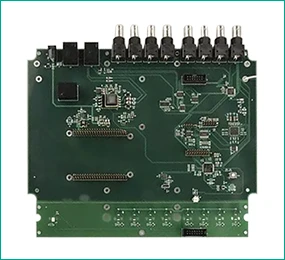
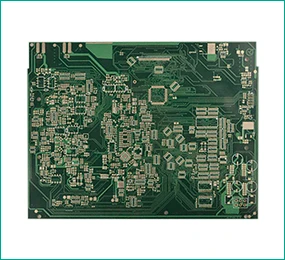
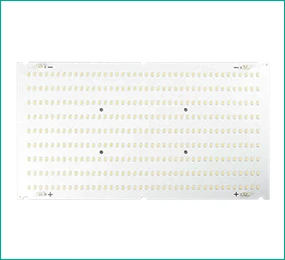
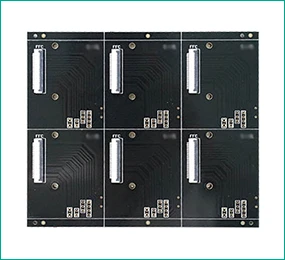