HDI PCB
From PCB design to mass production, MOKO provides one-stop HDI PCB manufacturing services to help customers shorten time-to-market and save costs.
Your Trusted HDI PCB Manufacturing Partner
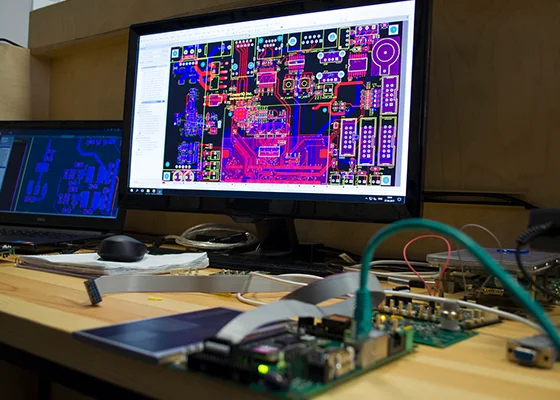
HDI PCB fabrication is rapidly becoming the ultimate solution for smaller, more efficient, and more durable PCBs. High-Density Interconnect (HDI) is a high-performance design that is characterized by its high density of components and routing Interconnections that use micro vias, blind and buried via or micro via techniques, and built-up Print Circuit Boards (PCBs) laminations.
As HDI PCBs specialist, MOKO Technology has extensive experience in manufacturing HDI PCBs for customers in different industries such as medical, automotive, and electronics. We have the ability to handle all HDI PCBs projects with unmatched accuracy and high quality within your budget.
Why Choose Us

High Quality
MOKO has a strict quality control system, we use various inspection methods to inspect each circuit board and even each component, working with us can save you from worrying about the quality.

Low Costs
We have a stable supply chain around the world, which enables us to get good materials at lower costs. In addition, all steps involved in HDI PCB manufacturing are completed under one roof which can save transportation costs.

Extensive Experience
We have been engaged in HDI PCBs manufacturing for about 17 years, serving customers from over 100 countries, our experienced engineers are well-versed in all types of circuit boards, and their expertise can ensure your project’s success.

Quick Delivery
Our one-stop manufacturing service allows us to better control the production schedule and deliver the HDI PCB within the time you require. In addition, we utilize industry-leading and highly automated equipment for production, which can significantly reduce manufacturing time.
Our HDI PCB Cases
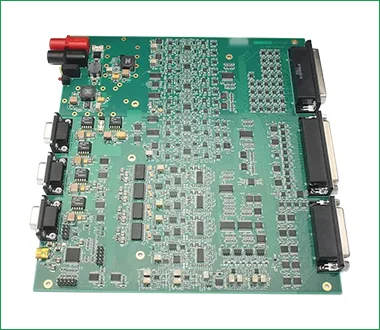
HDI PCBA Manufacturing
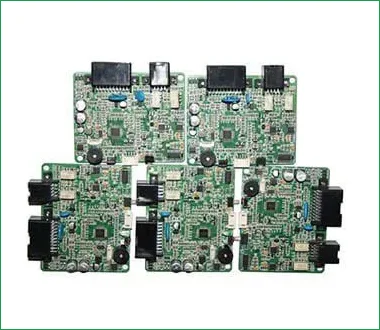
HDI PCBA for Monitoring System
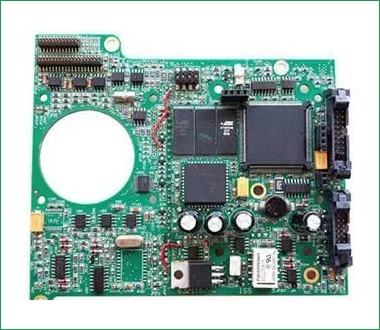
Industrial Controller HDI PCBA
Our Certifications
MOKO has obtained many certifications including ISO9001:2015, ROHS, BSCI, IPC, and UL, which demonstrates our commitment to stringent PCB quality control.
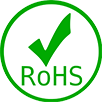
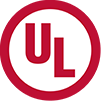
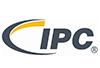

HDI PCB Specification at MOKO Technology
Layer
1 to 12 layers
Materials
FR-4, CEM-1, CEM-3, High TG, FR4 halogen-free, FR-1, FR-2, aluminum
Maximum Finish Thickness
0.2 to 4.0mm (0.02-0.25")
Maximum Finish Board Size
500 x 500mm (20 x 20")
Minimum Drilled Hole Size
0.25mm (10mil)
Minimum Line Width
0.10mm (4mil)
Surface Finish / Treatment
HALS / HALS lead-free, chemical tin, chemical gold, immersion gold, and plating gold
Copper Thickness
0.5 to 3.0oz
Solder Mask Colors
Green/black / White / Red / Blue
Inner Packing
Plastic bag
Outer Packing
Standard carton packing
Hole Tolerance
PTH ±0.076, NTPH ±0.05
Profiling Punching
Routing, V-cut, beveling
HDI PCB Applications
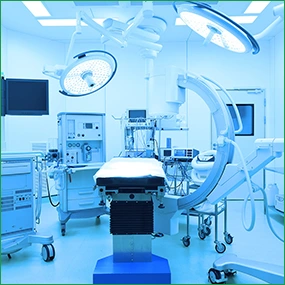
Medical Care
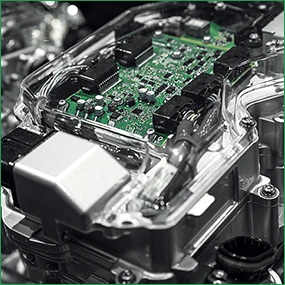
Automotive
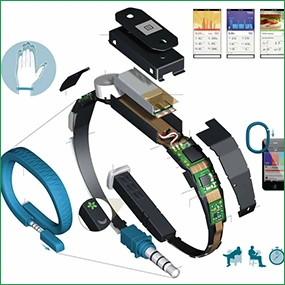
Electronics
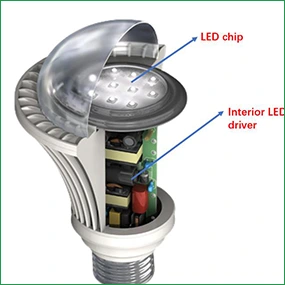
Lighting