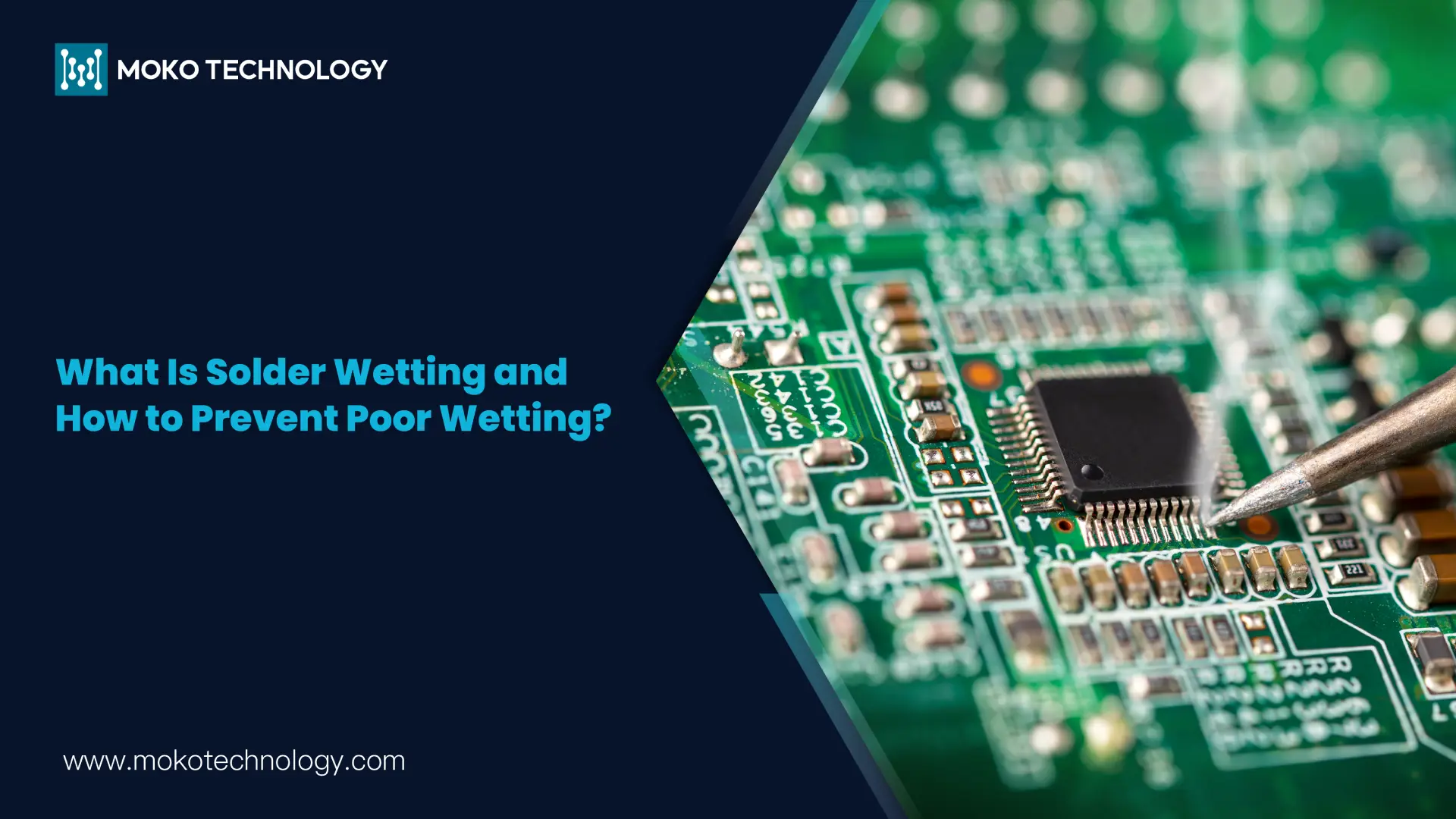
Soldering is a cornerstone technique in electronics assembly, it’s used to connect electrical pieces and mechanically attach them to a PCB (printed circuit board). A key step to this process
From PCB manufacturing to assembly, and testing, our one-stop services guarantee top-notch quality and customer satisfaction.
At MOKO, we pride ourselves on our rich experience in providing top-notch circuit board assembly services. From PCB manufacturing and components procurement to PCBA and testing, we offer comprehensive solutions to meet your needs. Our team of PCB industry experts works closely with you to ensure fast turnaround times and the highest quality results. Contact us today to discover how MOKO can take your PCBAs to the next level!
From PCB production, and component sourcing to assembly and testing, we can perform every step involved in the process well.
MOKO takes the quality of its products very seriously and 100% testing ensures that every PCBA delivered to our customers is of high quality.
MOKO has established a complete and reliable supplier network, which enables us to get qualified materials at competitive prices.
From prototypes, and small batches to high-volume production, and everything in between, we can deliver PCBAs within your deadlines.
We can source components from your nominated suppliers or our suppliers. We have a stable supplier network that allows us to obtain components and raw materials at a lower cost while maintaining high quality.
We are capable of manufacturing kinds of PCBs with different materials such as FR4 PCB, Aluminum PCB, heavy copper PCB, HDI PCB, etc. From single-layer, and double-layer to multi-layer PCBs, we can fabricate superior PCBs that can always meet your requirements.
MOKO has flexible assembly capabilities, we can complete PCB assembly within a short turnaround time. We provide various PCB assembly services including prototype PCB assembly,turnkey PCB assembly, PCB assembly rework, etc.
Before the delivery, we would apply a series of testing to check the quality and function of PCBA, the testing processes include in-circuit testing and 100% functional testing. We perform a visual inspection, automated optical inspection, and automated X-ray inspection.
Assembly Technologies:
Surface Mount Technology,Through Hole Technique,Mixed PCBA Technology,BGA Assembly
PCB Types:
Rigid, Flexible, Rigid-Flex PCBs, MC PCBs, Ceramic PCBs, Rogers PCBs
Parts Procurement:
Full Turnkey, Partial Turnkey, Consigned/kitted
Component Size:
Smallest Components, Micro BGA, Fine Pitch Parts Assembly
Production Capacity:
5 SMT lines, 3 DIP Production Lines, Produce 1.2 million pcs per day
Stencils:
Nano-coating, Laser-cut stainless steel
Soldering Types:
Reflow Soldering, Wave Soldering
Repair & Rework:
Ball Grid Array replacement, IR rework
Testing Methods:
AOI checking, Visual inspection, X-Ray checking, Flying Probe testing, ICT Testing, Functional Testing
“A reliable PCB and PCBA supplier. Very good customer support, Helpful, fast, and on-time delivery. I just wanted to say thank you for all of your help in getting these boards done.”
“Great quality of the Printed Circuit boards, the service was really good and the price was OK. A reliable PCB and PCBA supplier”
“When you work with MOKO, you are receiving high-quality PCB prototypes and production at affordable prices. Very good quality PCB manufacturer.”
Soldering is a cornerstone technique in electronics assembly, it’s used to connect electrical pieces and mechanically attach them to a PCB (printed circuit board). A key step to this process
Nowadays, electronic products are both compact and lightweight while performing a variety of functions. This is largely due to effective PCB thermal management. On the printed circuit boards, various components are
As technology continues to advance in the electronics industry, packaging remains one of the key success factors determining efficiency and reliability. One example of such technology that received considerable attention
PCB Assembly refers to the process of assembling all electronic components such as resistors, transistors, diodes, etc. onto a printed circuit board, and the assembly method can be manual or mechanical.
PCB is the bare board with conductive pathways. And PCB Assembly (PCBA) is the process of mounting the electrical components on the PCB so as to produce a working circuit.
These are the essential processes: solder paste application, pick and place, reflow soldering, inspection phase, through hole component insertion, wave soldering and finally testing.
SMT is best for compact, high-speed, and automated assembly needs. Through-hole assembly is preferable for components requiring strong mechanical bonds or in high-power applications.
It is principally used to generate functioning electronic circuit or equipment. PCB assembly provides for control of various components, interconnection to form a circuit, downsizing and enhance performance of electronic products.
The cost of PCBA is affected by various factors such as component types, order quantity, the number of components, labor costs, and so on.
Yes. MOKO is certified with ISO9001, ISO13485, ISO14001, IPC, and UL. Our factory and manufacturing process strictly follow industry regulations and standards.
Yes. We provide services ranging from prototypes to high-volume PCB assembly orders.
Sure, we can assemble PCBs with 1-40 layers.
Yes; we can supply lead-free components that comply with EU RoHS standards.
Yes, under the premise of quality assurance, we can deliver PCBA within 24 hours.
Yes, we can provide custom finish including OSP, ENIG, ImAg, ENIG, etc as your required.
Yes, we have the capability to do fin pitch down to 01005, and 0201 sizes.
Yes, we can install BGAm, MBGA, LGA.
Markets
Resources
Contact Us
Copyright ©2024 MOKO Technology | Your Trusted EMS Partner 粤ICP备15085690号