Design for Manufacturing
Our design for manufacturing services help customers shorten time to market and reduce manufacturing time and costs.
Outsource DFM Service to MOKO
Design for manufacturing(DFM), also known as design for manufacturability, is a process that aims to optimize the design of a part or product, making sure the final product can be highly performed and more cost-effective.
MOKO Technology has extensive experience in designing, product development and manufacturing. We provide full-scale services ranging from concept design, engineering to prototyping and production, so we understand how important a great DFM service is, how it can affect the subsequent processes. We not only focus on the aesthetics in our designs but also care about the cost and functions when it comes to high-volume manufacturing. Thus, we can help our customers save more costs and create better products to improve their market competitiveness.
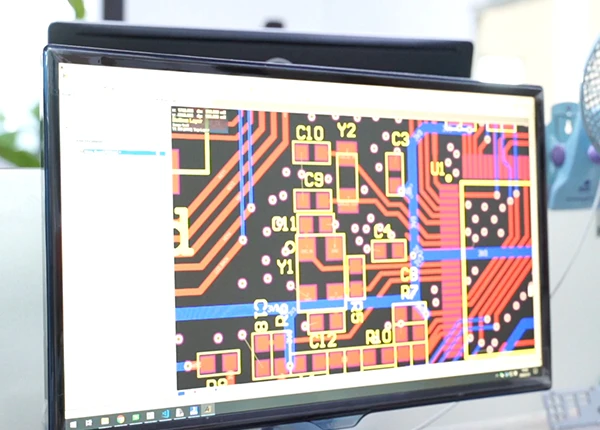
Our DFM Services
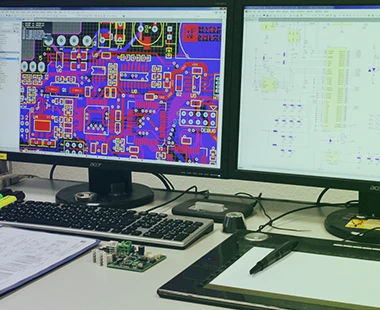
Optimize Design
Use the latest CAD tools to develop models of concepts, provide design solutions to customers based on existing infrastructure, and ensure that your products are manufactured in a cost-effective manner.
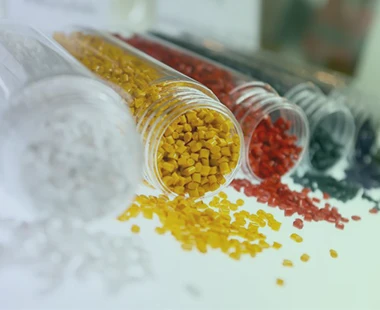
Select Suitable Materials
According to customer needs, MOKO can help you choose the best material for each part of the product to meet various properties such as strength and toughness.
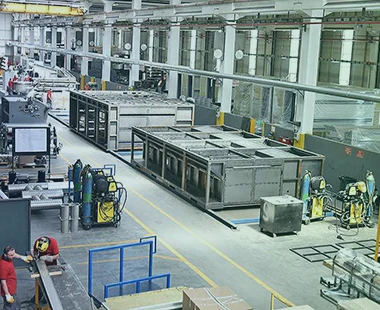
Manufacturing Feasibility
For high-volume manufacturing, our engineering team conducts on-site testing to ensure your concept is ready for fabrication and assembly, with a best effort to optimize cost and eliminate defects.
Benefits of Design for Manufacturing
Quality Control
DFM can identify manufacturability problems in the product design stage and provide suggestions for solving the problems, avoiding the situation where problems are discovered after the product has been officially put into production, and reducing the risk in the process of new product development. In the DFM process, it is also possible to evaluate whether the design tolerance of the product is reasonable, to ensure the reliability and the quality of the product.
Shorten Turnaround Time
The process of DFM can optimize the product by simplifying or reducing the manufacturing operations and part quantities, which can shorten product development cycles significantly. In addition, identifying potential manufacturing issues during the initial design phase can prevent redesign at later stages, which can also save more time.
Decrease the Total Cost
During the process of design for manufacturing, the cost and availability of materials would be discussed and analyzed to figure out if any other alternative materials are more cost-effective. Furthermore, the optimized manufacturing process can reduce the cost as well.
Why Choose Us

Extensive Experience
Engineers at MOKO are well-educated and professional who have offered DFM solutions to customers in a variety of industries such as aerospace, automobile, communications and medical.

Information Confidentiality
We protect intellectual property, and we abide by a non-disclosure agreement. The data and design that our customers shared with us will never be disclosed to a third party.

Effective Communication
We speak the same language as you, literally and figuratively, so we can understand your requirements well and respond quickly to facilitate work and ensure that all processes run smoothly.
Five Principles of Design for Manufacturing
Optimize Design
It is vital for us to choose a correct manufacturing process, for instance, we shouldn’t use a highly-capitalized process to make a low-volume part. And we also need to take tolerances and materials into consideration.
Design
All designs should follow manufacturing principles. Generally speaking, simple designs are preferred as they have lower risks than complicated designs. And the design should cover every aspect, especially some details like tolerance, thicknesses and consistency.
Materials
Material for manufacturing would significantly impact the cost and quality of the final product, so when choosing materials, we should understand the properties of each material including its mechanical and thermal properties.
Environment
When designing a product, we should consider the environment in which the final product will be used. And every operating condition should be considered to make sure that the products can perform well in these conditions.
Testing
We have to test every aspect of the product, making sure that each product and component can comply with industry standards, safety and quality standards.
Design for Manufacturing FAQs
Design for Manufacturing (DFM) refers to the practice that aims to optimize a product’s design to ensure that it can be manufactured with high efficiency and cost-effectiveness.
They have different purposes, Design for Manufacturing (DFM) aims to improve the design so as to optimize the manufacturing process, while Design for Assembly (DFA) focuses on simplifying the assembly process such as designing a PCB in a way that makes the assembly of components easier, faster, and more reliable.
The key consideration in DFM is the spacing and tolerances between components, traces, and vias.
In PCBA, the process of design for manufacturability includes design review, manufacturability analysis, component placement optimization, solder joint design verification, assembly process planning, test point accessibility check, thermal management assessment, documentation and feedback.
Because it helps avoid common design issues and further prevents problems such as costly revisions and delays. In addition, it ensures that the design aligns with the manufacturing capabilities and limitations
DFM-compliant design means fewer design changes and production errors, which leads to lower manufacturing costs and also quicker turnaround times.
These problems include narrow trace width, improperly designed via, closely placed components, incorrect hole size and non-suitable materials for the fabrication process.
To get the best quality, MOKO Technology’s DFM service should be sought at the early design stage when the layout of the PCBs are being done to avoid costly revisions.
Yes, MOKO Technology has expertise in handling complex designs, including multilayer PCBs, HDI PCBs, and high-density assemblies, ensuring they meet both design and manufacturing requirements.
Currently, we support Gerber, ODB++ and IPC 2581 for PCB DFM review so that we provide you with the full check of your design.
Ready to Get a Quote?
Want to know more about our DFM service? Contact us to find out how we can help your next project.