Medical Electronics Manufacturing
MOKO Technology is ISO13485 certified, we are committed to providing the most reliable medical electronics manufacturing solutions.
Medical electronics play a crucial role in modern healthcare, which contributes to advancements in medical technology, improves patient care, and enables more accurate diagnoses and efficient treatments. It is because they are closely related to people’s lives and health that they must be manufactured according to the strictest industry standards to ensure high reliability. MOKO Technology provides integrated manufacturing solutions for leading medical device companies, from PCB assembly, and component procurement, to finished product assembly, and testing. We keep up with the ever-changing market trends, introduce industry-leading technologies, and provide customers with cutting-edge medical electronic products. Under the premise of ensuring product quality, we have the ability to respond quickly and can help customers quickly bring products to the market.
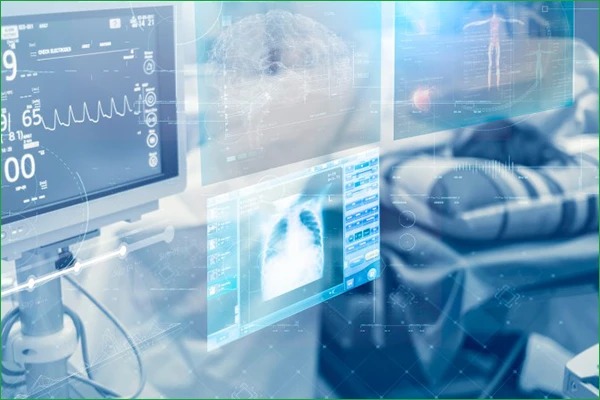
Play Video about Design & Engineering
Our Medical Electronics Manufacturing Services
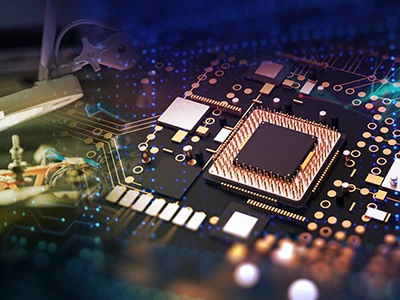
Design and Engineering
• PCB Design
• Free DFM Check
• BOM Review
• Rapid Prototyping
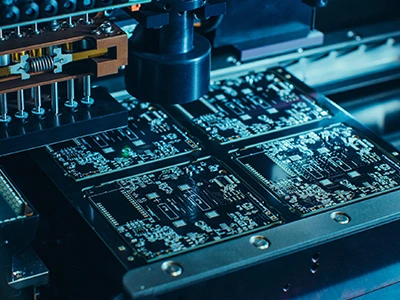
Advanced Electronic Manufacturing
• PCB Manufacturing
• PCB Assembly
• Integrated Manufacturing
• Cable Wire Harness Assembly
• Electromechanical Assembly
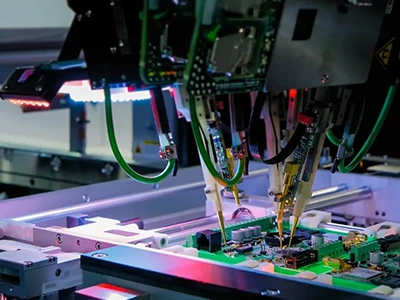
Testing and Inspection
• Incoming Quality Control
• Customized Electronic Testing
• EMC Test
• Functional Test
• Sampling Audit
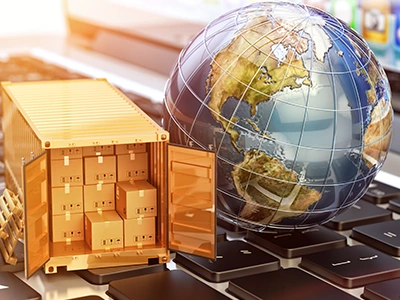
Value Added Services
• Component Sourcing
• Supply Chain Management
• Logistics
• Product Certification Assistance
Electronics Manufacturing Capabilities at MOKO
Manufacturing Capabilities Overview
• 13000 square meters production area
• 100% ESD components control
• 5 SMT lines+ 3 DIP lines
• 30,000 square meter PCB Per Month
• 100,000,000 Units of PCB Assembly Per Month
• CNC 5-Axis, 7-Axis, and Multi-Axis Machining
• Laser Welding
• Ultrasonic Welding
• Fusion of many materials – metals and plastics
• Hermetic Enclosure Capabilities
• Injection Molding
• 3D Printing
Certifications
• ISO 9001
• ISO 14001
• ISO 13485
• UL
• IPC
• RoHS
…
Why Choose MOKO Technology

Lean Manufacturing
As an expert in consumer electronics manufacturing, MOKO is always compliant with industry regulations and stringently controls the quality of each product. We are certified to industry certifications including ISO 9001, ISO 14001, and UL standards.

Quality Assurance
MOKO is a leading electronics manufacturer in China, we have a professional team covering engineering, fabrication, and sales that would provide 24/7 service to support our customers, making sure all problems can be solved with satisfaction.

Supply Chain Management
We have strong and flexible manufacturing capabilities, which enable us to efficiently manage production across various scales, from prototypes, and small batches to high-volume production, and everything in between.

Competitive Prices
Our in-house manufacturing allows us to control costs and quality effectively. Our state-of-the-art automation equipment enhances productivity and reduces labor costs, enabling us to offer cost-effective products to our customers.
Our Proven Cases

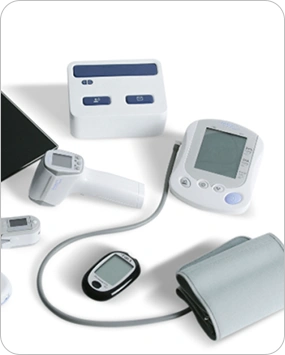
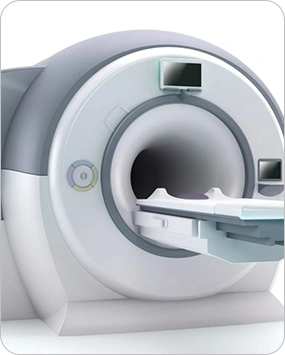
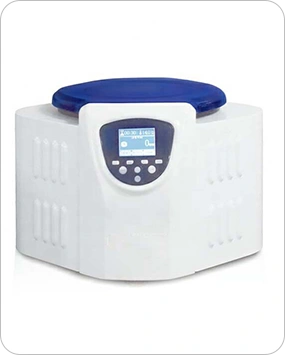