Die Casting
Die casting is an automated casting process that forces molten metal such as zinc, copper, aluminum, magnesium, lead and tin into a mold cavity with high pressure and high speed. The molds are also called tools or dies, which are designed especially for each product, so it can fabricate metal parts with high accuracy. It is a prefect technique for making small and medium-sized metal parts in large quantities.
MOKO Technology is specialized in die casting technique, we have top-tier casting machines including hot-chamber and cold-chamber die casting machines, and we have offered die casting services for many projects ranging from different industries like electronics, healthcare and automotive.
Why MOKO Technology?
The First-class Facility
Over the years, MOKO has invested a lot of costs to update equipment to reach the industry-leading level. Our excellent melting system gives us the confidence to handle a variety of alloys, our hot-chamber and cold-chamber die casting machines make sure that we can produce highly accurate and consistent metal parts for our customers.
Quality Assurance
MOKO Technology has obtained certifications including ISO9001:2015, ISO14001, ISO13485, ROHS, BSCI, and UL, our fabrication process and products are qualified to international standards. We put our clients into the priority, making sure our products and service can meet if not exceed their requirements.
Rich Experience
MOKO Technology has been established in 2006, which is composed of skilled engineers and well-trained workers. We have professional knowledge and extensive experience, and we have provided casting services to a lot of customers around the world.
Amazing Service
MOKO Technology is committed to offering the best customer services to our clients, our friendly and professional sales team is 24/7 available to offer the best solution and quick response to our customers.
Die Casting Cases at MOKO Technology
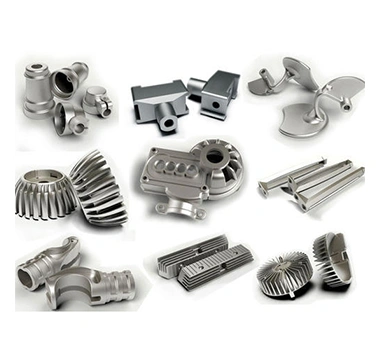
Aluminum alloy castings
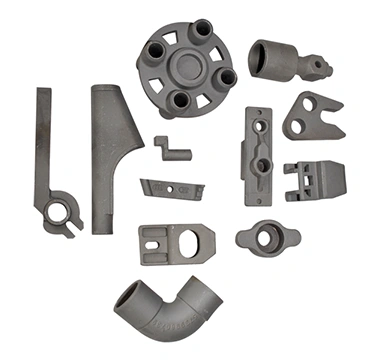
Automobile
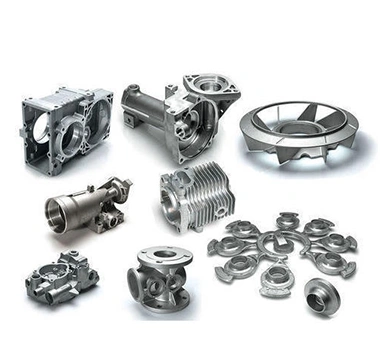
Die cast automotive parts
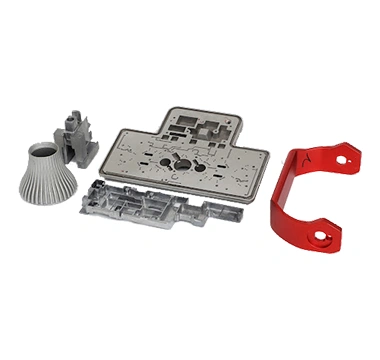
Die Cast Metal Parts

Ductile iron casting parts
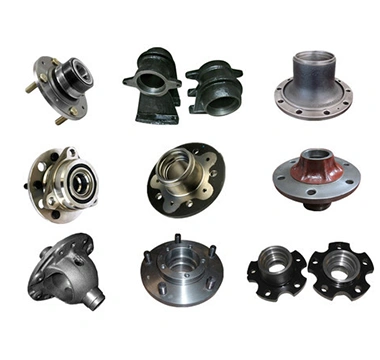
Investment casting
The Advantages of Die Casting
High Accuracy: The die-cast process makes sure that the metal parts are made with precise dimensions, and the parts from different batches can be uniform and consistent only if the mold is not changed.
Good Performance: Die-cast products are featured with high corrosion resistance, high strength and hardness and durability, as there are no welded parts.
High Production Efficiency: Its short cycle time and automation allow the manufacturer to fabricate thousands of metal parts quickly, and there are no extra processes needed.
Versatility: It can be applied to produce metal parts with different alloys and various shapes even some complex shapes.
Die Casting Processes at MOKO
Hot-chamber Die Casting
Hot chamber casting, also known as gooseneck machine, is a process that has a quick cycling time(about 15 cycles per minute). It is suitable for low-melting alloys such as zinc and magnesium. The feature is that the metal is heated in the casting machine as there is a built-in furnace to melt metal, and the molten metal would be finally forced at high speed and high pressure into the mold through the gooseneck. But we should notice that the hot-chamber die casting is not suitable for aluminum, as it would carry iron out of the molten pool.
Cold-chamber Die Casting
When you hear the name “cold-chamber”, you must wonder that if such a process is carried out in a cold environment? The answer is no. We still need to melt metals, but the furnace is not built-in. Before we start cold-chamber casting, we need to melt metal in a separate furnace, and transport a precise amount of molten metal into the cold-chamber machine(the temperature of the chamber is the room temperature), and then it would be forced into the die by a hydraulic or mechanical piston. Cold-chamber die casting has a slower cycle time and it is perfect for high-melting alloys such as aluminum.
Hot-Chamber Die Casting VS Cold-Chamber Die Casting:
Temperature Range: Hot-chamber die casting is suitable for low-melting alloys and the maximum temperature it can handle is around 450°C. While the cold-chamber die casting can handle metal alloys with a temperature of about 600°C.
Furnace Location: The furnace is built inside of the hot-chamber machine, but for the cold-chamber machine, the furnace is separated.
Production Time: Hot-chamber die casting has a faster cycle time than cold-chamber die casting that requires manual operation of the molten metal.
Tool Life: Hot-chamber machine has a longer lifespan as it handles low melting alloys, which has less impact on the machine.
If you are not sure which one is the best choice for your project, contact MOKO today to get a professional answer!
Choose Us for Better Services Always
Interested in getting a free quote? Please take a minute to contact us and we will get back to you within 24 hours.