
Short Turnaround Time
If your project timeline is tight, you are in the right place. MOKO offers fast sheet metal forming services, making sure we can always catch your schedule.

Custom-tailored Metal Parts
Sheet metal fabrication capacities at MOKO Technology allow us to manufacture kinds of metal parts ranging from simple to complicated ones.

Full Range Services
In addition to sheet metal parts, we provide services like in-house welding, powder coating, and assembly, making sure we can meet your different requirements well.
Sheet Metal Forming Services at MOKO Technology
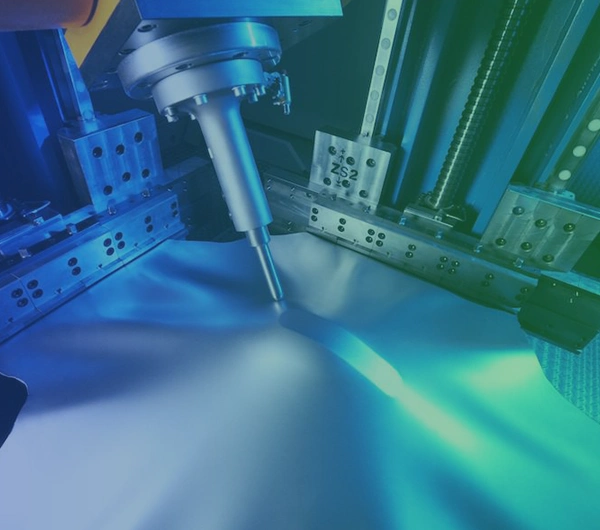
Sheet metal forming is a manufacturing process that aims to modify the sheet metal into the desired shapes by applying forces to them. During this process, the sheet can be formed with different shapes without changing its material composition and volume, it can be applied to fabricate different metal parts, with weight from hundreds of grams to tons. It has a wide array of applications, from the architecture industry to the automobile and aerospace industries.
MOKO Technology offers one-stop sheet metal forming services to our customers, which is featured with a short development period, quick production turnaround time, and premium products with durability and high accuracy. We have accumulated rich experience since our establishment in 2006, so we can handle a variety of sheet metal forming projects, from simple shapes to complex shapes, from prototype to low- and high-volume.
Our Sheet Metal Forming Gallery
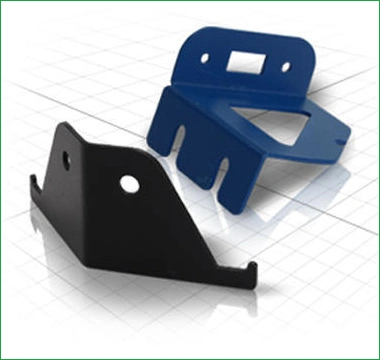
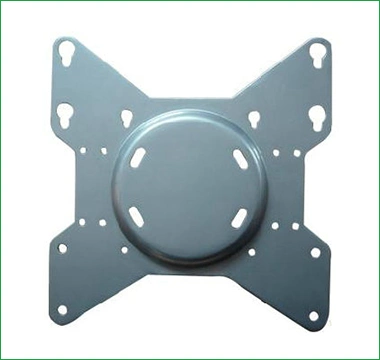
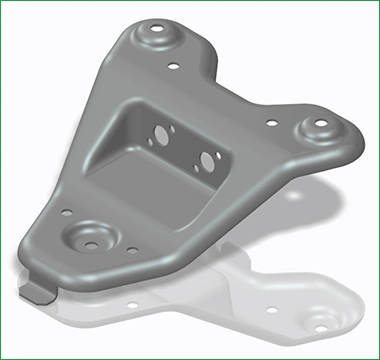
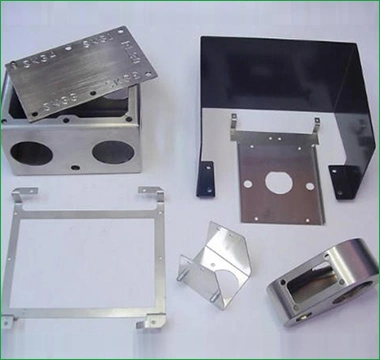
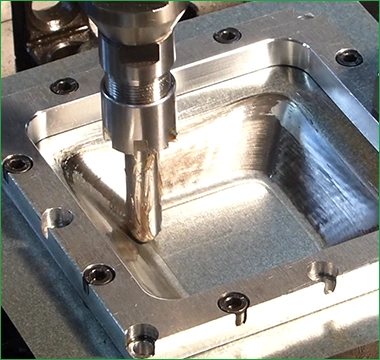
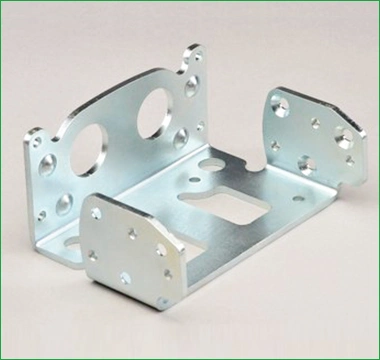
Sheet Metal Forming Methods
Stamping
Stamping is a method that forms sheet metal into different shapes. How does it work? First, the flat sheet metal would be placed into the stamping press, and then the tools and die would apply pressure to it and finally form the flat sheet with desired shapes. Stamping can produce complex metal parts in a short time, but it requires high-tonnage presses.
Bending
Bending is a process that applies pressure to change the shape of sheet metal, which is hard to achieve by manual and it requires to use machines such as press brakes and machine presses. The sheet metal would be out into a die and then the punch applies pressure to it to form the specific shape.
It sounds easy, but actually, it is more complex. During the bending process, the “spring back” problem may occur (it refers to a phenomenon that the sheet metal tries to regain its original shape after bending), and to avoid such a problem, overbend is needed that makes sure the final product can be made with the exact shape even after the occurrence of the “spring back” . So it is of vital importance to choose a professional manufacturer who can handle this technique well.
Hemming
Hemming is a technique that folds or folds the edge of the sheet metal onto another part to achieve a perfect fit, the hemmed sheet metal has nice edges with no burrs or other defects. There are at least 2 steps during hemming, the first step is to bend the sheet metal into a V-shape, the second step is to take out the sheet metal and flatten the hem by putting it into a flattening die. The hemming process must be operated precisely and professionally, which would impact the surface appearance and quality.
Deep Drawing
Deep drawing is a very popular sheet metal forming technique, during the process, the sheet metal is drawn radially into the forming die by the mechanical action of the punch, which is a forming technique that combined with stretch and compress processes. Deep drawing is a very cost-effective process as fewer material is used or wasted, widely used for automobile components fabrication.
Advantages of Sheet Metal Forming
High Accuracy
At present, CAD and CNC technology is applied in sheet metal forming, which is very intelligent and efficient. The CNC punch presses can be programmed to control the movement and positioning of the sheet metal, and the punch tolerance is no more than 0.05mm.
Durability and Versatility
Sheet metal forming techniques can be applied to various metal materials and shapes, which offers engineers more choices when developing new and creative projects. In addition, the sheet metal formed products are durable and strong enough to be exposed to unfavorable environments such as bad weather and chemical corrosion.
Cost-effective
At present, sheet metal forming is the most cost-effective forming process especially for high-volume projects, as the whole process is highly automatic that can reduce the labor cost significantly. And the material waste during forming is less, which can also cut the total cost. On the other hand, the process requires only a few steps, so the production efficiency is pretty high, which can improve the production capacity.
Ready for a Free Quote?
Want to know how our sheet metal fabrication services can set you apart from your competitors? Well, take a minute to contact us, our professional and friendly team will show you the answer.
- All uploads are secure and confidential