
Short Turnaround Time
If your project timeline is tight, you are in the right place. MOKO offers fast sheet metal cutting services, making sure we can always catch your schedule.

Custom-tailored Metal Parts
Sheet metal fabrication capacities at MOKO Technology allow us to manufacture kinds of metal parts ranging from simple to complicated ones.

Full Range Services
In addition to sheet metal parts, we provide services like in-house welding, powder coating, and assembly, making sure we can meet your different requirements well.
Sheet Metal Cutting Services at MOKO Technology
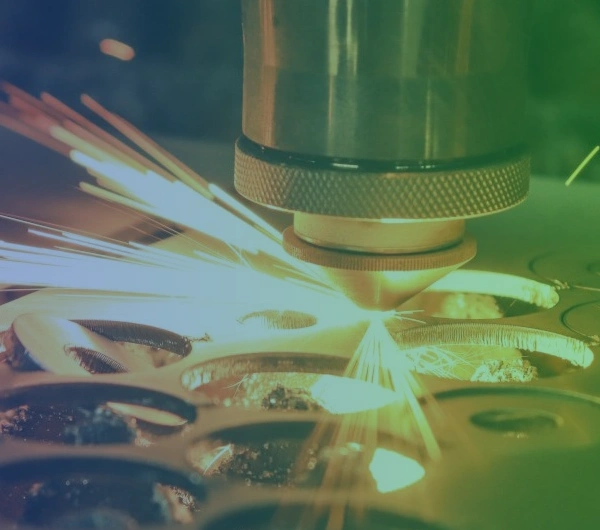
Sheet metal cutting, true to its name, is a process that would cut a part of materials to meet the design requirement of final products, which is considered a subtractive fabrication process. And it is widely used for production with high volumes due to its high production efficiency.
MOKO offers one-stop sheet metal fabrication services including design, cutting, forming and so on. Thanks to the advanced sheet metal fabrication equipment such as mechanical presses and cleaning systems, MOKO is confident to supply our clients with precisely cut sheet metal without blanking burrs or other defects. We have rich experience in sheet metal cutting services and our engineers are the experts in this area, we can handle a variety of materials weight up to thousands of pounds including aluminum, carbon steel, iron, manganese, nickel-based alloys, etc.
Sheet Metal Cutting Cases at MOKO Technology
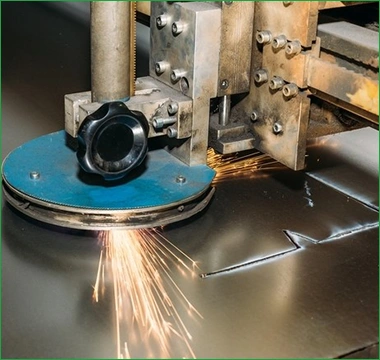
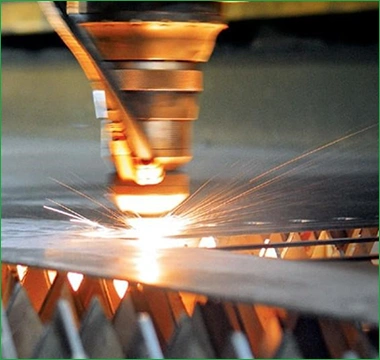
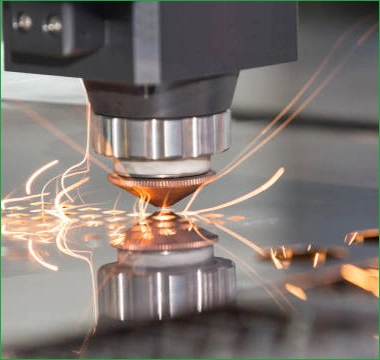
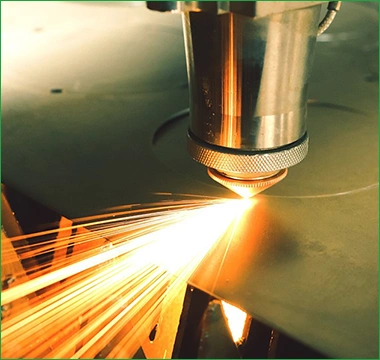
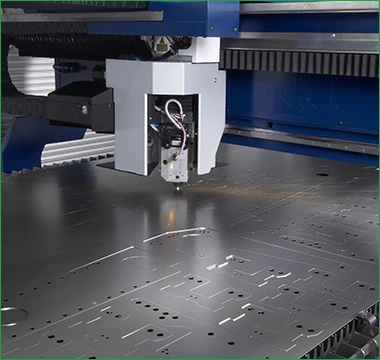
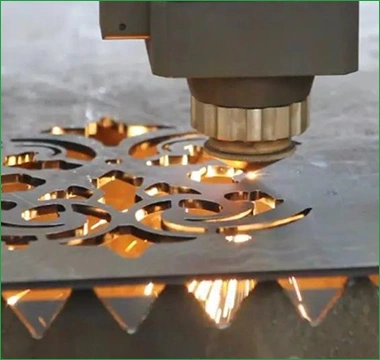
MOKO Sheet Metal Cutting Techniques
MOKO Technology provides various sheet metal cutting techniques, and generally speaking, there are 2 main types of the cutting technology: cutting with shear forces, and cutting without shear forces. Let’s check more details of each type below:
Cutting with Shear Forces
Applying shear forces during sheet metal cutting is a commonly used technique, which is also known as the “shearing process”. When the shearing force is large enough, the material would be separated from the metal sheet and finally we can get the sheet metal with the required size and shape. So how does it work? Normally, there are 2 tools that would be located above and below the sheet metal, then the tool above would quickly punch the metal plate that is located above the below tool to make the fracture of the metal sheet. The cutting effect is depended on several factors, including the sharpness of tools, the material and thickness of the metal plate.
Cutting without Shear Forces
In addition to shear forces, there are many other forces can be used for cutting processes, such as thermal energy, pressure, abrasion, ect. At MOKO Technology, there are 3 typical sheet metal cutting techniques that use no shear forces but other forces, let discuss them one by one:
Water Jet Cutting
The water jet cutting technique cuts metal sheets by applying high pressure( about 60,000 psi ) and high speed water flow(around 2000ft/s), and the water contains some abrasive to cut sheet metal better. The metal sheet cut by this technique is featured with smooth surface finishes, no burrs. In addition, it can reduce the chance of deforming due to the heat as it is quenched with water through the whole process.
Laser Cutting
Laser cutting is a process that uses high powered laser beams to remove the extra sheet material away. These beams would be centralized on the sheet metal, then the heat they emitted would help to vaporize and finally cut the material. This cutting technique can be used for various materials, it is efficient, productive and cost-effective.
Plasma Cutting
The plasma cutting technique is only workable for electrically conductive materials. During the cutting process, the plasma cutter would generate charged beams of compressed ionized gas to blow the unwanted materials away. The material would be heated up until it is molten, which would cause rough cut edges, burrs, and other defects. So plasma cutting is suitable for those projects that apply thick metal sheet, which has low requirements for the surface finish as well.
The Comparison of Different Sheet Metal Cutting Techniques
Water jet cutting, laser cutting, and plasma cutting are all sheet metal cutting techniques without shear forces, each of them have their pros and cons. For your better understanding, we list more details in the below chart:
Cutting Types
Advantages
Disadvantages
Water Jet Cutting
1.Various materials available
2.High precision
3.Nice surface finishes
4.No HAZ
1.High cost
2.Larger kerf width
Laser Cutting
1.Wide range of materials available
2.Better functionality(workable for making marks)
3.Fewer burrs Small deformation
1.With HAZ
2.High cost
Plasma Cutting
1.Lower cost
2.Suitable for thick material
1.Rough surface finishes and cut edges
2.Material limitation
3.With HAZ
If you are not sure what kind of cutting technique is the best choice for your project, do not hesitate to get in touch with us, our experts would offer help to you throughout.
Ready for a Free Quote?
Want to know how our sheet metal fabrication services can set you apart from your competitors? Well, take a minute to contact us, our professional and friendly team will show you the answer.
- All uploads are secure and confidential