In addition to green PCB, the blue circuit board is the second most common type used in the electronic field. Today, we are going to introduce what it is, how it is classified, its history and advantages as well as the manufacturing process.
What Is A Blue Circuit Board?
When it comes to blue printed circuit boards, we should know that the blue dye is on its solder mask. Also, it is one of the most popular types in the electronic industry.
The Material Composition of Blue Printed Circuit Board
The material composition of Blue PCB contains substrate, copper foil, solder mask and other auxiliary materials. What makes the board blue is the blue dye applied on the solder mask. As for the blue color, this is usually achieved by using a specific environmental corrosion agent, such as the blue sodium persulfate, which reacts with copper to produce copper ions to turn blue when the PCB is corroded.
Different Types of Blue PCB
The blue circuit board is a common sub-type of PCB. However, for the classification of this sub-type PCB, we can use lots of methods. For example, based on material, blue PCB can be classified into paper substrate type, glass fiber substrate plastic and plastic substrate. In addition to grouping by materials, we can organize them by construction. There will be four types- single layer board, double layer board, multiple layer board and flexible layer. Besides, there will be high-frequent board and high TG board if we classify blue board by usage.
Why Are Circuits Blue?
With the development of electronic industry, blue circuit board becomes more and more frequent-used in the market where there was only green PCB before.
History and Evolution
At the early stage, the only consideration on solder mask design is reducing soldering. As time goes by, PCB industry become more mature, and PCB optimization penetrates into every tiny aspect, including the color of solder mask. Gradually, blue PCB features in the market with its excellent stability and visual effect.
Advantages of Blue PCB
Blue circuit board really makes a positive effect on PCB manufacturing process. It has such good contrast ratio in vision that machine and workers in product lines can identify the layout and component on the board with ease. This greatly improve the quality of the final product. Besides, blue circuit board background comes with good luminousness, which allows thorough pass of ultraviolet light in the process of exposure. Last but not least, it is very suitable to apply blue PCB in LCD, since they are in the same color.
Blue vs Green Circuits Board
Compared to traditional green circuit board, blue PCB differs a lot. First, it is costly since it is not common as green one. Before starting blue board production, manufacturer has to revise equipment parameters in the product line in order to adapt the color change. This costs extra labour fee, so blue PCB is more expensive than green PCB.
Second, blue PCB provides different visual effect from green one. While green PCB shows great contrast between board and circuit routine, blue circuit board background matches to the color of LCD a lot and offers a coordinating appearance of the whole LCD device.
How Are Blue PCB Manufactured?
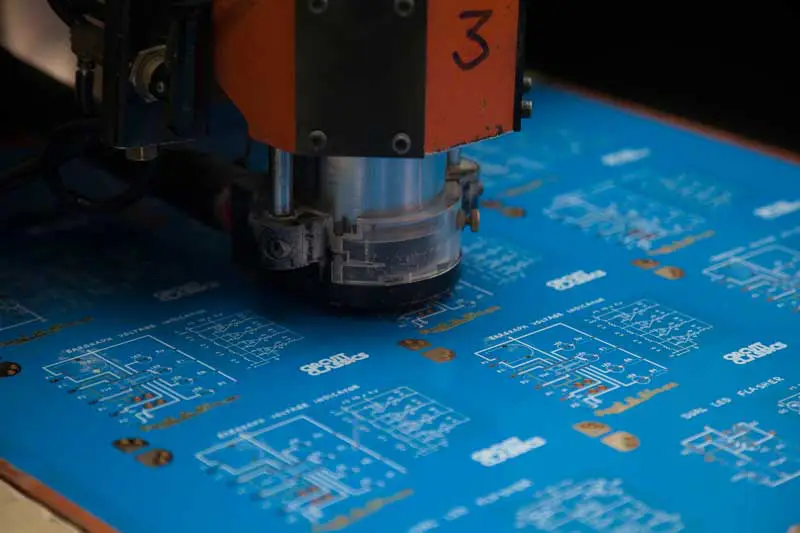
The manufacture process of blue printed circuit is similar to common green PCB, but more attention should be paid to film pressing, exposure, development and inspection process.
During film pressing, we should precisely control parameters of production technique so as to form a flat and smooth blue mask. This plays an significant roles in the circuit process.
In the process of PCB exposure, factory should adjust the parameter of exposure machine, including exposure time and intensity, in order to transfer the pattern clearly and accurately.
During exposure, it will takes longer time and stronger developing solution to ensure that exposure part is reserved and other part is completely removed. Furthermore, due to the special color, factory has to make hard effort to take inspection and quality control by adopting excellent testing equipment and methods.
How to Pack Blue PCB?
After finishing batch production, blue printed board should be packed by special materials with good shading properties. And, it should be stored in shade site, because blue substrate is sensitive to UV light. Moreover, the packing materials should be in stable chemical properties to prevent chemical reaction and penetration against blue ink. Some factory may take more measures like testing package materials to ensure right packing.
Application
Blue circuit board is widely applied in computer, server, network device , telecommunication device and industrial control equipment. Its reliability exactly fits it into the above field. If you are confused about whether you should make blue PCB for your device, please feel free to contact us. We are pleased to offer professional helps.