MOKO Insert Molding
Insert molding is one of the most effective molding techniques, which can combine metals and plastics together into a molded part firmly and perfectly. It is much popular and widely used for many applications such as encapsulated electronic devices, threaded fasteners, medical equipment and so on. MOKO Technology has been working on it for over a decade, we offer one-stop insert molding solutions, ranging from designing to manufacturing, finishing and after-sales services. We specialize in molding products, not only for insert molding, but also for conventional molding, over-molding and injection molding, etc.
Why Choosing MOKO Technology for Insert Molding?
Extensive Experience
At MOKO, we have participated in a multitude of insert molding projects since its establishment in 2006, our engineers are experts in this area who can help you throughout the project to provide the custom-tailored solution to you.
Quality Assurance
Over the years, MOKO has invested a lot of costs to update equipment to ensure that our equipment reaches the industry-leading level. Our advanced machines have better production performance that can also guarantee the quality of our products.
Premium Quality
MOKO has obtained certifications including ISO9001:2015, ISO14001, ISO13485, ROHS, BSCI, and UL, which means our manufacturing process and products can meet the international standards. You are free of the quality problem, our strict quality control department can make sure that the products our customers receive are top-tier.
Industry-leading Insert Molding Service
Over the years, MOKO has been evolving our equipment and optimizing the process to ensure that our molding services reach the industry-leading level. Our advanced machines have better production performance that can also guarantee the quality of our products, and the optimized process improves the production efficiency significantly.
Insert Molding Products Display

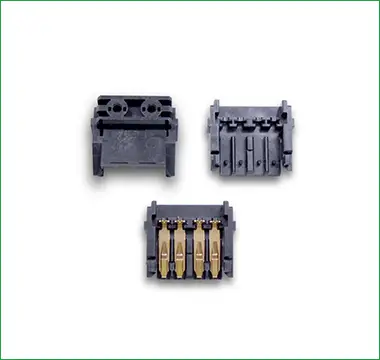
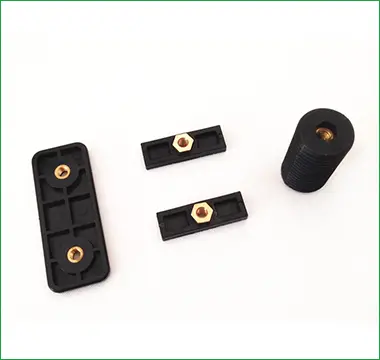
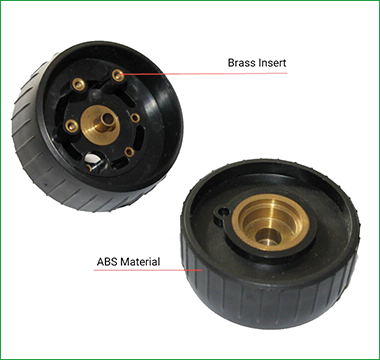
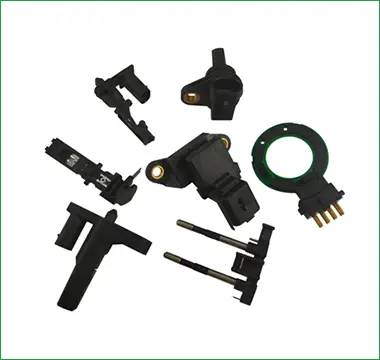
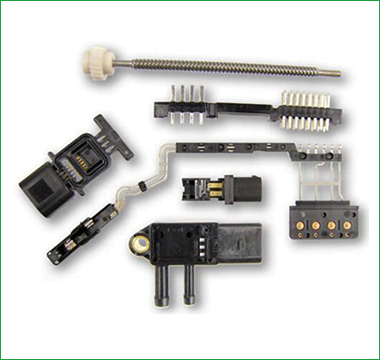
How Does Insert Molding Work?
The insert molding process is roughly the same as the production steps of traditional injection molding, the main difference is that the metal part would be placed in the mold at the specific position first for insert molding, and the method of inserting metal parts can both be a manual and automatic way. The following lists each step of the whole process:
The first step, insert the metal part into the mold in the correct position. For production with low volumes, we can use manual insertion, but please note that manual insertion has the limitation of metal sizes. Normally, the operators need to wear gloves as the high mold temperature, which would bring inconvenience to operation, especially when the metal parts are tiny. While for automatic insertion, it has high accuracy, consistency and efficiency. But we should aware that the initial cost for an automatic process is much higher, so we should choose one method that is most cost-effective.
Second, the molten plastic material would be injected into the mold, and cover the metal part completely when it solidifies, making sure that these metal and plastic components can be adhesive firmly and perfectly.
The last step, remove the well-encapsulated components from the mold after cooling.
The Advantages of Insert Molding
Smaller Product Sizes
Compared with assembly parts, insert molded products has smaller sizes as the metal part is located inside, which means the size of the whole product can keep the same even equipped with metal components. On the other hand, the insert molding process can manufacture smaller and thinner components while the performance will not be affected.
Lower Costs
There is no need to assemble parts, no welding or other secondary process required for insert molding, only the metal part insertion may require the manual operation, which can reduce assembly and labor cost largely. In addition, some economical materials such as resins are workable for it, so that the whole cost can be lowered.
Less Error
The process involves a few steps and it is highly automatic, which reduces the possibility of making errors. The whole process is well-designed and the robots guarantee the high accuracy of products.
More Material Options
There are a variety of materials that can be used for insert molding, for example, thermoplastic materials like polyethylene, polystyrene, and nylon, which are recyclable, light and durable. In addition, materials like epoxy and rubber are also workable for inset molding.
Design Flexibility
Insert molding can make the designing job easier, as the engineers needn’t think about how to design the assembled parts. On the other hand, it can fabricate components with various shapes and materials, which will not limit the design ideas and can expand possibilities of making different molded parts for different industries.
Want to Start Injection Mold Project Today?
We offer high standard injection molding services, support low volume manufacturing, fast delivery, and quick respond within 24 hours.