CAPABILITEIS
Selective Laser Sintering Service
- Short Turnaround Time within 24 Hours
- A Variety of Materials Available
- Complex 3D Printed Part with High Performance
Why Choose MOKO?
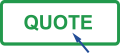
Instant Feedback
Just provide your CAD file to us, we will make quick responses about prices and manufacturability within 24 hours.
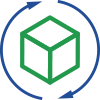
From Prototype to Production Runs
Thanks to our industry-leading equipment and proficient workers, we are capable of manufacturing 3D parts from prototypes to large production runs at a fast speed.
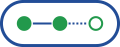
Quality Assurance
Certificated with ISO9001, MOKO fabricates 3D parts that can always reach the international standard and set our customers assured.
Selective Laser Sintering at MOKO Technology
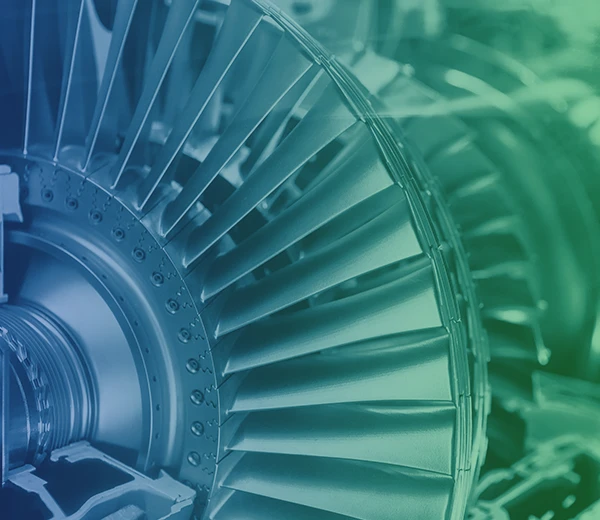
MOKO Technology offers one-stop selective laser sintering services, supplying 3D parts with high accuracy and performance to our clients. Our engineers have rich experience in SLS technology who can optimize your design through CAD and handle SLS projects with a variety of materials and applications. The industry-leading SLS printers we used can guarantee the quality of our products and improve the productivity significantly for not only the prototype, but also for large volumes.
We offer the instant quote and feedback for your selective laser sintering projects, we can fabricate 3D parts as fast as 1 workday, and our professional and friendly sales team is 24/7 online to make sure you can get the satisfying service. We have obtained certifications including ISO9001, ROHS, BSCI, and UL, our SLS process and 3D parts are qualified to international standards.
Our Selective Laser Sintering Cases
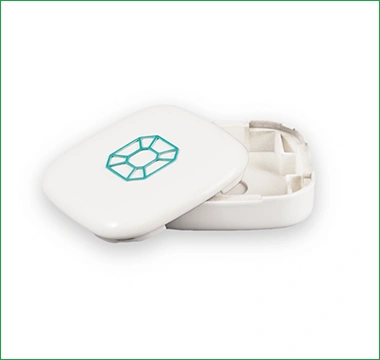
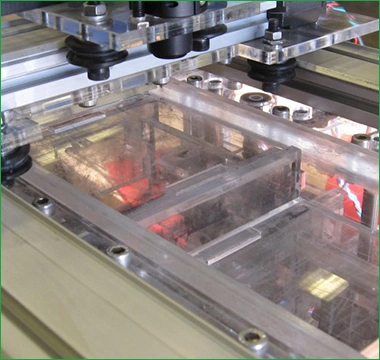
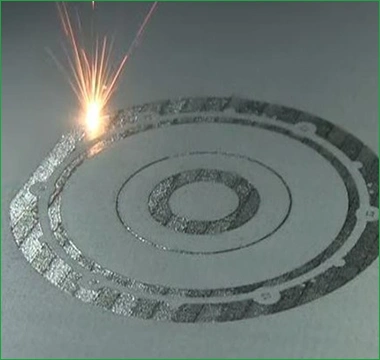
What is Selective Laser Sintering?
Selective laser sintering is a 3D printing technology that manufactures 3D parts by applying laser beams to sinter powder at the specific positions and bonding them layer by layer until forming the final solid component that is defined by CAD data. It is a cost-effective technology with high productivity that is workable with various materials such as elastomeric thermoplastics, nylon, polystyrene, which makes the SLS become one of the most widely used 3D printing technology. The common applications of SLS include medical devices, automotive components, parts with snap fits, electronics and so on.
How Does Selective Laser Sintering Work?
Step 1: Loading the powder into the printer and then heat the powder and construction area to a temperature that is below the melting temperature of the raw material. This step can help to raise the temperature of specific regions of the powder bed and solidify parts easier.
Step 2: Laser beams would be applied at the specific positions and powder would be fused together and form a solid layer. Then the build platform would be lowered by about 50 to 200 microns so there are more room for forming other layers, the processes mentioned above would be repeated until the final 3D model is finished. In this process, the unfused powder can be used to support the part, so there is no need to make support structures.
Step 3: When the printing is finished, it need to take some time for the build chamber to cool down, which can avoid the problem of warping in components and help to optimize the mechanical properties.
Step 4: Taking the final part out of the printer, and to get a beautiful 3D model, the final step is to remove the excess powder that can be reused. In addition, in some projects, other post-processing is required to make a more pretty surface and appearance.
The Benefits of Selective Laser Sintering
Design Flexibility
Selective laser sintering is featured with great design flexibility, which requires no support structure, while other 3D printing technologies such as SLA and FDM need. It can be used to fabricate components with complex geometries including some interlocking structure or those parts with interior channels that could not be fabricated by any other technologies.
Short Turnaround Time
Selective laser sintering enables engineers to apply the machines and materials used in prototyping to produce the end-use products, which can significantly shorten the product development cycle as there is no need to find other materials or methods. On the other hand, there is no support structure required for the SLS process, so the total fabrication speed would be faster.
High Performance 3D Parts
Selective laser sintering produces robust and compact 3D parts that have great performance no matter for prototyping or end-use applications, and the SLS 3D parts from MOKO are featured with high accuracy, good surface finish and also durability that makes sure you can use them for a long time.
Various Materials Available
There are a variety of materials workable for selective laser sintering technology, and the SLS materials portfolio can meet all your requirements well, no matter you require heat resistance, flexibility, or other properties.
Lower Cost
Selective laser sintering has a lower cost when compared with other 3D printing technologies, as it has material efficiency, high productivity, highly automatic tools and no complex post-processing required.
Start Your 3D Printing Project with an Expert
Whether you require turnkey solutions or customized 3D projects, we are here to help you out. Feel free to call us at 86-75523573370 to discuss your project today!