MOKO Plastic Injection Molding
With 6000 square meters of factory building space, MOKO can provide a full range of plastic injection molding services to our clients, including in-house injection molding fabrication, DFM engineering, tool designing and building, surface finishing, painting and assembly, etc. In addition, MOKO has wide plastic molding capabilities such as insert molding, overmolding and structural foam molding.
Our experts in this area would work with you closely throughout the project, from the concept design to engineering and fabrication, they would offer useful suggestions and workable solutions that can always meet your expectations.
Until now, we have over 10 years of experience in injection molding and serving customers in different industries, our extensive project experience and professional knowledge can shorten the project turnaround time and guarantee the product quality to improve your company’s market competitiveness.
Why Choosing MOKO for Plastic Injection Molding?
- Quality assurance, MOKO is certificated withSO9001:2015, ROHS, BSCI, and UL
- Fast turnaround time, making sure our customers can receive products on time
- Professional knowledge and extensive experience
- Competitive prices thanks to our in-house manufacturing
- Amazing customer service, we make quick response to you within24 hours
The Advantages of Plastic Injection Molding
High Production Efficiency
The process of plastic injection molding is highly automated, unlike the human, machines can work continuously without break as long as there is no failure of machines. So the production efficiency is quite high and is well-suited for mass production.
Workable for Complicated Parts
It supports to create a part with different geometric shapes from simple to complicated ones. More importantly, there is less finishing work required as the plastic injected products look like finished, what we need to do is just to make sure the feasibility of the design.
A Wide Range of Materials Available
We are allowed to choose a wide array of materials for plastic injection molding, we can even mix different materials to achieve specific properties, which is called co-injection molding.
Cost-effectiveness
The plastic injection molding requires few operators as most processes are automatic, thus, the labor cost is reduced. On the other hand, there is little waste during the process as the excessive materials can be recycled, which saves the material cost.
Product Display
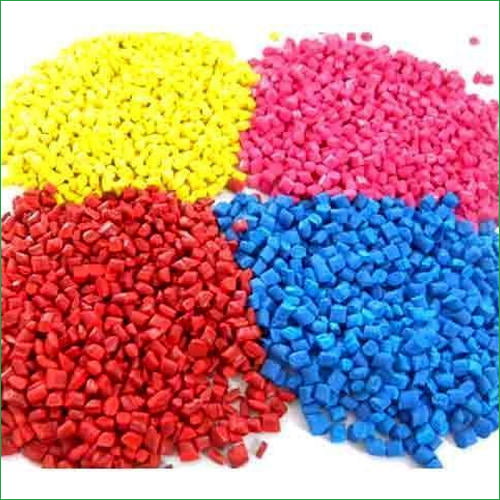
Plastic Master Batch
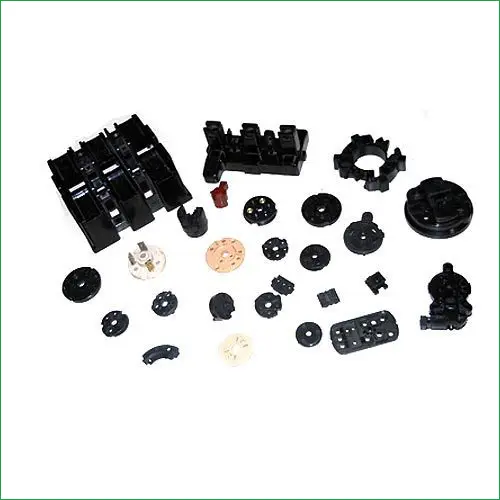
Injection Molded Compontents
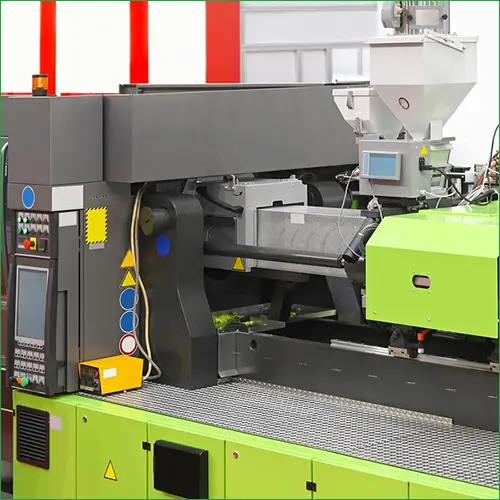
Injection Molding Press
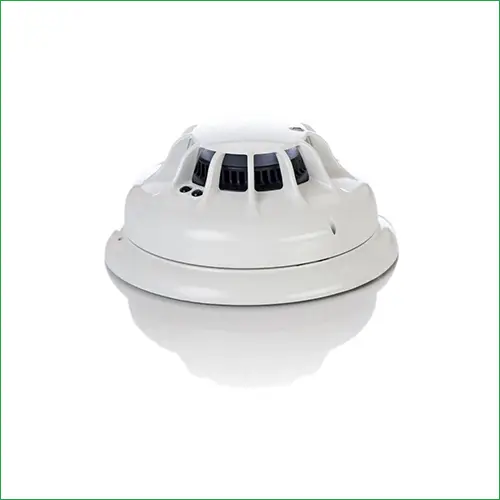
Smoke Alarms
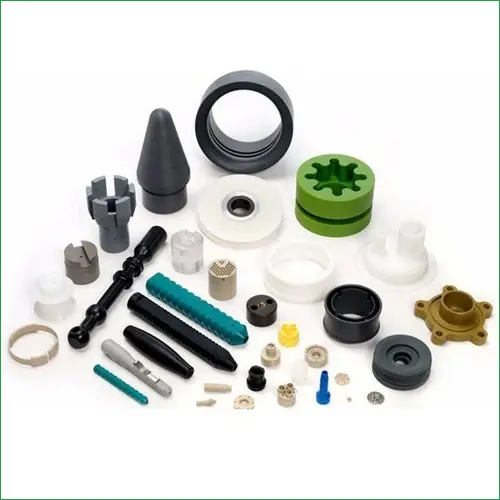
Plastic Injection Moulding Components
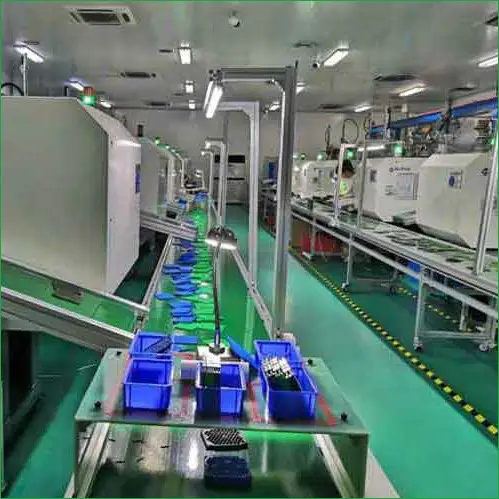
Production Line Injection Molding Machine
What is Plastic Injection Molding?
Plastic injection molding is a manufacturing process that can produce identical plastic components in large volumes. There are many plastic materials available for this process, and the most commonly used materials are thermoplastic and thermosetting polymers. It is very popular that is widely used in different industries, such as automobile, medical, aerospace, consumer electronics and so on.
How Does Plastic Injection Molding Work?
Plastic injection molding is not easy work, every step matters.
STEP 1: Feed Materials
At the first step, the plastic material would be fed into a heated barrel and mixed by using a helical-shaped screw.
STEP 2: Injection
The plastic material would be heated and molten into a liquid state that would be injected into the mold. At this time, the displaced air would be exhausted through the vents of the injection pins and the parting line.
STEP 3: Cooling
When the plastic material cools sufficiently, it solidifies and forms a shape that matches the shape of the mold. Cooling time is decided by the material used and the thickness of the plastic components. The mold is designed with cooling or heating lines inside, and water is circulated through the mold to maintain a constant temperature.
STEP 4: Ejection
The mold opens and ejector pins would eject the part from the mold, and the part would fall in a bin located below the mold.
STEP 5: Recycling and Packaging
In the last step, we would classify the usable parts and other materials that can be recycled to lower the cost, while the usable parts would be packed.
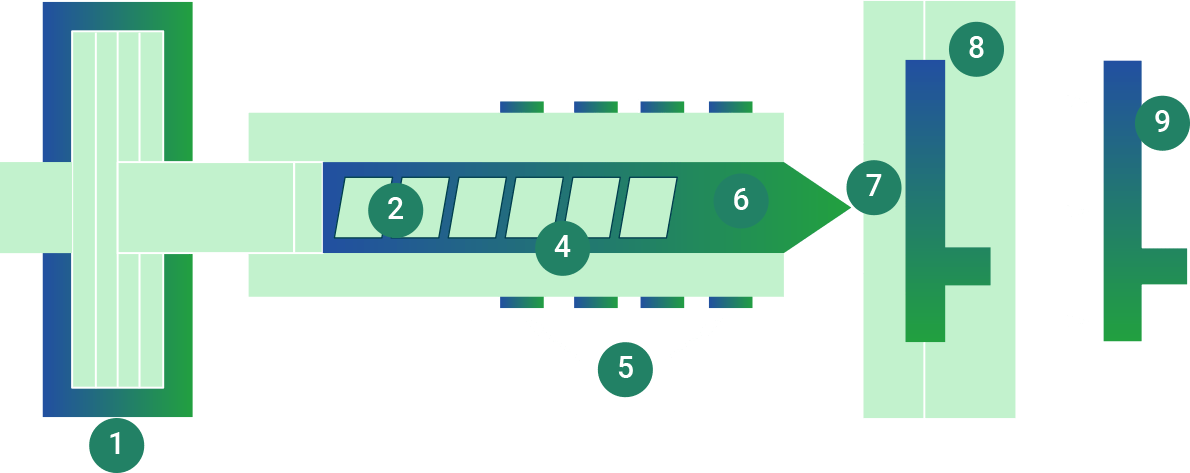
Start Your Plastic Injection Mold Project Now!
If you have any plastic injection mold projects or want to know more about our services, please contact us now to see how we can set you apart from others.