CNC stands for computer numerical control, which is a technology to control the machining tools automatically by applying a microcomputer that is attached to the tool. CNCs machines would operate according to the coded programmed instructions, such as the movement of the machines, the feed rate of materials, the speed, and so on. There is no need for operators to control the machine manually, thus, CNC helps to improve the efficiency and precision to a large extent.
From the 1940s when the first numerical control machine was developed to 2022, CNC technology has been constantly developing and plays a vital role in different industries. In this blog, we will explain more details about this technology including how CNCs work, different processes for CNC machining, its advantages, etc. Let’s read on…
How Does CNC Work?
In a CNC system, microcomputers are used to perform all basic functions based on the program that is loaded in the machine control unit, which can send commands to the servo drive to achieve a variety of functions such as turning on&off the motors and coolant, changing tools and pallet. In addition, all operations of CNCs are monitored continuously by feedback devices such as proximity sensors, pressure sensors, and so on. So if there is any error, the system would generate a “Fault Message” to alarm the operator.
Types of CNC Machines
CNC Mills
Normally, CNC mills consist of a three-axis system, that is X, Y, and Z axes, and some advanced mills can accommodate three additional axes. This kind of machine is able to run on programs consisting of numeric and letter-based prompts, which can guide workpieces across different distances. As to the programming, both G-code and other unique languages developed by the manufacturing team can be used for milling machines.
Lathes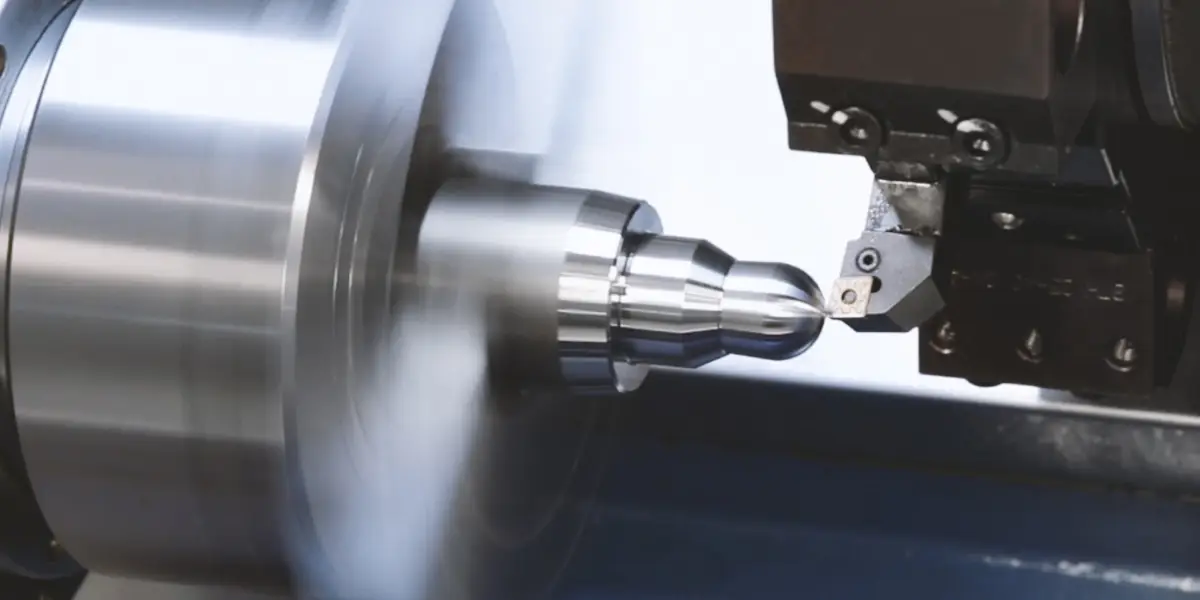
CNC lathes can perform high-precision and high-speed cutting, and lathes would cut the workpieces in a circular direction by using indexable tools. Lathes have similar functions as CNC mills, and they can also be controlled by G-code and other unique code, but lathes consist of only 2 axes(X and Z axes). CNC lathes are suitable for manufacturing complicated products that cannot be achieved manually.
Plasma Cutters
CNC plasma cutters are mostly used for cutting metal materials and can be applied to other surfaces in a few cases. During the cutting process, compressed-air gas and electrical arcs are combined to generate plasma that can provide enough speed and heat to cut metal.
CNC Electric Discharge Machines
Electric-discharge machining (EDM) is a process that molds workpieces into a specific shape by using electrical sparks.
During the machining process, continuous electrical discharges between two electrodes can remove the unwanted materials of the workpiece. In EDM, the material would be placed in between two electrodes, and then the amount of electrical discharge that each electrode needs to produce would be calculated by machines.
CNC Laser Cutter
It works similar to CNC plasma cutters, and the only difference is that laser cutters can be used for kinds of materials like metals, plastic or hardwood. The intensity of the laser can be adjusted according to different materials used that have different densities and strengths.
CNC Router
A CNC router is a very practical machine that uses the computer to control the cutting machine, it can be applied for a wide array of materials such as steel, wood, aluminum, plastic and so on. Compared to other machines, it has higher productivity and less waste by manufacturing different items within a short time.
CNC Machining
FIND OUT HOW TO SELECT THE RIGHT CNC MACHINING FOR YOUR PROJECT
There is a variety of materials workable for CNC machining including plastics, metals, wood, glass, and so on, making it a very popular technology in a wide range of industries like automobile, medical, electronics, telecommunications, etc.
CNC Machining Steps
- Step 1: CAD Model Design
In the first step, we need to design a 2D or 3D CAD model, which is usually done by using computer-aided design software, and the information such as dimensions and geometries of the product would be included in the CAD file.
- Step 2: File Conversion
In the second step, we need to convert the CAD file to a CNC-compatible file format, usually is “G-code”, so the CNCs machine can recognize it. Here, we would use the computer-aided manufacturing (CAM) software to run this kind of file runs, which would generate the digital programming code to control these machines.
- Step 3: Machine Setting
We need to set up machines before they start to work. For instance, we need to test the speed and positioning, making sure their performance is good. And we need to attach the tools required to the proper machine components. It is a very important step, as wrong settings would damage machines and parts as well.
- Step 4: Machining Operation Execution
In the last step, CNCs machines would start to work according to the commands sent from the program, and each movement of machines and tools would strictly comply with the program. So the final products made by CNC machining would be exactly the same as the original design.
Common Processes for CNC Machining
CNC Milling
In the CNC milling process, the rotating multi-point cutting tools are utilized to remove the extra materials and manufacture a part with a specific shape. The whole process is controlled by computers to ensure the high precision of the parts. This process can be used for rapid prototypes and finished components as well.
The milling process is not complicated: First, we need to design a CAD model that can be both 2D and 3D. Second, transfer the CAD file to “G-code” so CNC machines can recognize it. Last, set the CNC milling machine and start to work. Learn more about CNC milling>>
CNC Turning
CNC turning is usually done on CNC lathes or turning centers by the combination of the rotary motion of the workpieces and translatory motions of the tools to remove the unwanted materials. CNC turning is a very cost-efficient technology that has high material removal rate, it can be used to cut wood, metal, and plastic. CNC lathes have a simpler mechanical design than CNC milling, which cost less when producing the same parts.
The Advantages of CNC
High Production Efficiency
CNCs machines can perform a series of actions automatically, what we need to do is to program and set machines. There are only a few steps involved, and more importantly, these machines can work 24/7 without breaking only if there is no failure of the machine. So it can improve production efficiency hugely.
Consistency and Precision
Compared to manual machining, CNCs machines are controlled by computers that help to eliminate manual errors and improve the accuracy and consistency of products in different batches. So CNC is very suitable for those projects that have high requirements about the quality and reliability of products.
Cost-Effectiveness
Though the initial costs for CNCs machines are high, their high productivity and lower rate of manufacturing errors make them a cost-effective choice for many manufacturers. Think about it, how much would cost if there are any human errors that may cause rework or repair? In addition, there is less human labor required during the process, a proficient operators can run several machines at the same time. CNCs technology is becoming more and more popular, which can also help to reduce the cost of these machines.
Available for Various Parts
CNC is featured with versatility that can be applied for different parts. On the one hand, it can manufacture parts with different shapes from simple to complicated ones with high accuracy. On the other hand, we can reprogram the CNCs machines to manufacture a completely new part with a short turnaround time.
MOKO Is Your Reliable CNC Partner
MOKO has offered extensive CNCs services to our customers for over 10 years, ranging from CAD model design, CNC milling, CNC turning, to surface grinding, and after-market service. Our experiences and expertise make sure that we can always offer high-quality CNCs processing and products for our clients.
We can design solutions and carry out them with successful results with a short turnaround time. At MOKO Technology, we utilize multi-tasking tools and multi-axis CNCs machines including 3-, 4- and 5-axis CNCs machines, which help us to manufacture parts in different materials with high accuracy and efficiency, we are capable of handling CNCs projects for different applications and meeting the growing technical needs of customers. We streamline our process and upgrade our equipment to constantly improve our productivity, we can manufacture prototypes, low- and high-volume production runs in a very short time.
This blog is a primer for CNCs technology, hopefully, it can help you to know CNCs technology better. If you are interested in getting more information or want to start your CNCs projects, please contact us.